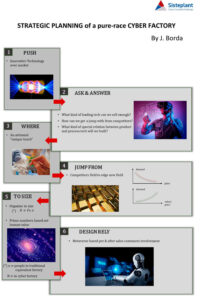
STRATEGIC PLANNING of a pure-race CYBER FACTORY
10 Competitive Technology Orbitals in a Cyber Factory
SHARE ON
Incluir en nuestras reflexiones estratégicas líneas de actuación que permitan lanzar productos y servicios adaptados a la demanda de nuestros clientes, es algo entendido y asumido por muchas industrias. Sin embargo, el reto es cómo lograr estas fabricaciones en series cortas y establecer los pasos a dar para crear personalizaciones en masa de forma rentable y sostenible. Hablar de personalizar es hablar de cómo nos aproximamos a nuestros clientes desde un valor diferencial de nuestros productos o servicios. O lo que es lo mismo, cómo anticiparnos a las necesidades del mercado, ampliando nuestra oferta de valor de forma inteligente.
La diversificación bien entendida tiene su origen en el punto anterior, a la hora de acometer un proyecto de este tipo podemos enfrentarlo con dos perspectivas. Entrada en sectores nuevos con el producto tradicional, lo cual puede hacernos ganar volumen, pero no necesariamente rentabilidad o, por el contrario, pensar en cómo entrar en mercados nuevos que “premian” el producto fabricado de forma más personalizada, en serie corta y con un mayor aporte de valor y por tanto más rentabilidad para la compañía.
Todo un desafío que tiene dos grandes titulares: agilidad extrema y capacidad de adaptación eficiente. Para acometerlo, será necesario poner muchas ganas en el proceso de transformación, realizar cambios en nuestros procesos y dotarnos de herramientas que tendremos que implantar tanto internamente como de cara a nuestra relación con terceros.
Desde la concepción del producto podemos pensar en variantes controladas que permitan ampliar de forma robusta la gama de productos que fabricaremos o crear funcionalidades adicionales una vez que esté en uso por parte de nuestros clientes. Un buen proceso de configuración de producto será clave para lograrlo. Pero luego hay que fabricar, y aquí es donde empiezan los grandes retos y la necesidad de replantear nuestros procesos productivos y el modelo de gestión de nuestras compañías.
Nuestro plan de transformación interno deberá contemplar varias de las siguientes reflexiones: Replantear el proceso de industrialización, de donde todo parte, y que muchas veces asumimos que debe ser largo. En este nuevo contexto los modelos tradicionales no son válidos, la agilidad y robustez mandan. Flexibilizar los medios de fabricación tradicionales, de forma que podamos reaccionar optimizando costes y asegurando niveles de calidad y rendimiento óptimos. Analizar nuestras tecnologías actuales, así como la configuración de los equipos productivos. Ensayar nuevas tecnologías y aprender de esta experimentación para poder incorporarlas de forma robusta cuando sea necesario.
También, transformar nuestros medios productivos para que sean modulares, huyendo de la gran instalación e intentando en todo momento que las líneas de producción futuras sean reconfigurables (física o virtualmente ). Desarrollar, además, una planificación y programación que permitan reaccionar de forma ágil en entornos de trabajo multi-referencia. Los sistemas pull tradicionales, no dan respuesta en un entorno de personalización. Existen otras formas de organizar los procesos que contribuyen a mejorar la sincronización. Igualmente es necesario implantar sistemas que nos permitan pasar de una trazabilidad por lote a un control unitario.
Finalmente, dominar el proceso, primero entender cómo se comportan los activos y qué variables influyen en este comportamiento. Después, implantar sistemas de monitorización en tiempo real, para posteriormente sacar el máximo partido de la inteligencia artifical. La IA nos permitirá configurar un proceso de forma rápida, corregir y predecir una desviación durante el proceso de fabricación o prevenir una avería. Este proceso que garantiza un flujo de información tecnológica útil desde y hasta los procesos críticos y auxiliares es la “Sincronización Tecnológica Explícita”.
En el caso de Sisteplant, una vez definida la estrategia y desarrollados los procesos soporte necesarios, la implantación de nuestra Suite Manufacturing Intelligence nos permite: sincronizar procesos y aplicar el concepto de células virtuales, implantar el concepto de reconfigurabilidad de flujos e instalaciones, optimizar la fiabilidad, disponibilidad de medios y desarrollar las capacidades tecnológicas de las personas que intervienen en el proceso.
De cara al exterior también hay líneas de trabajo, como implantar herramientas que permitan predecir la demanda, proceso habitualmente poco trabajado en las organizaciones industriales. Nos conformamos con replicar modelos de años anteriores con escasas modificaciones que tan solo tienen en cuenta la estacionalidad. Aquí de nuevo los algoritmos pueden ser de gran ayuda, ya que pueden ayudarnos a identificar cambios en los modelos de consumo o detectar cómo ciertos factores coyunturales, sociales o económicos van a influir en nuestros negocios.
Mejorar la integración de nuestras cadenas de suministro, asegurando una transmisión rápida a nuestros proveedores de los diferentes escenarios de demanda, la identificación de ‘cuellos de botella’ y potenciales ineficiencias, así como una resolución ágil de las mismas.
Contribuir al desarrollo de nuestros proveedores, ya que nada haremos con acometer nuestro proceso de transformación si no ayudamos a nuestros proveedores a organizar su propio modelo de transformación adaptado a series cortas.
Por último, para tener éxito en este proceso de transformación, no olvidemos que tenemos que asegurar que existen canales internos para que nuestro equipo humano crezca, activando la creatividad en toda la organización, generando valor en torno a los activos intangibles de la empresa, asegurando una gestión dual que armoniza los planes a corto con la estrategia a largo plazo.
Por: Ana Santiago, CEO Sisteplant.
10 Competitive Technology Orbitals in a Cyber Factory
10 Competitive Technology Orbitals in a Cyber Factory
10 Competitive Technology Orbitals in a Cyber Factory
This website uses cookies so that we can provide you with the best user experience possible. Cookie information is stored in your browser and performs functions such as recognising you when you return to our website and helping our team to understand which sections of the website you find most interesting and useful.
Strictly Necessary Cookie should be enabled at all times so that we can save your preferences for cookie settings.
If you disable this cookie, we will not be able to save your preferences. This means that every time you visit this website you will need to enable or disable cookies again.
This website uses Google Analytics to collect anonymous information such as the number of visitors to the site, and the most popular pages.
Keeping this cookie enabled helps us to improve our website.
Please enable Strictly Necessary Cookies first so that we can save your preferences!
More information about our Cookie Policy