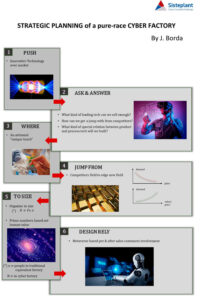
STRATEGIC PLANNING of a pure-race CYBER FACTORY
10 Competitive Technology Orbitals in a Cyber Factory
SHARE ON
Texto traducido original “The Machine Awakens”, Traducido por G Translate.
El mantenimiento industrial se ha enfrentado desde hace tiempo a las paradas imprevistas y a los elevados costes de reparación. Los enfoques reactivos reparan las máquinas solo cuando fallan, mientras que los métodos preventivos reemplazan piezas según plazos estrictos, a menudo innecesariamente. El mantenimiento predictivo introdujo información basada en datos que detecta fallos con antelación; sin embargo, aún se requieren decisiones humanas para programar y realizar reparaciones. Ahora, está surgiendo un paradigma conocido como mantenimiento cognitivo, en el que las máquinas contribuyen activamente a su propia salud. El mantenimiento cognitivo va más allá de las simples alertas, ya que permite a los activos autodiagnosticar problemas y responder dinámicamente, reduciendo las averías y prolongando su vida útil. En lugar de funcionar hasta que algo se rompe, las máquinas se adaptan a los factores de estrés y se coordinan con otros sistemas para optimizar el rendimiento.
El mantenimiento cognitivo depende de múltiples tecnologías convergentes que van más allá de la monitorización pasiva hacia la acción autónoma, incluyendo los gemelos digitales cognitivos, la computación de borde, la propiocepción y la robótica autoconsciente, el metaverso industrial y el mantenimiento orientado a misiones. Al integrar estos elementos, el mantenimiento cognitivo representa una nueva forma de garantizar la fiabilidad industrial, la rentabilidad y la sostenibilidad a largo plazo.
Los gemelos digitales tradicionales son copias digitales pasivas de activos físicos. Pueden reflejar las condiciones actuales y proporcionar análisis, pero rara vez tienen la capacidad de aprender o evolucionar. Los gemelos digitales cognitivos se actualizan continuamente mediante la asimilación de nuevos datos de sensores, registros de mantenimiento y retroalimentación del operador. Utilizan este conocimiento para optimizar el funcionamiento de un activo físico y predecir las necesidades de mantenimiento.
En lugar de simplemente enviar alertas a técnicos humanos que planifican las reparaciones, los gemelos cognitivos inician intervenciones y ajustes de forma autónoma. Mientras que el mantenimiento predictivo se centra en detectar señales tempranas de fallo, el mantenimiento cognitivo adopta un enfoque más amplio.
Al combinar la IA con la experiencia en ingeniería y el contexto operativo en tiempo real, el sistema puede decidir si una máquina debe recibir mantenimiento de inmediato o si puede seguir funcionando de forma segura, alineando así las decisiones de mantenimiento con los objetivos de negocio. Dado que estos gemelos pueden procesar grandes volúmenes de lecturas de sensores a una velocidad excepcional, ayudan a evitar reemplazos prematuros de piezas y averías catastróficas. Como resultado, las industrias se benefician de un nuevo estándar de fiabilidad y ahorro de costes.
Los gemelos digitales cognitivos representan la unificación de tres dominios tradicionalmente separados: tecnología de la información para la gestión de datos, tecnología operativa para el control sobre el terreno y tecnología de ingeniería para los aspectos mecánicos y de diseño de los activos. Al combinar estos dominios, los gemelos cognitivos generan información en tiempo real que va más allá de la detección de problemas. Estos coordinadores inteligentes orquestan las actividades de mantenimiento, adaptan el comportamiento de las máquinas y maximizan su vida útil sin la supervisión constante de técnicos humanos.
La computación en el borde contribuye al mantenimiento cognitivo al permitir el procesamiento instantáneo de datos a nivel de activos. En escenarios donde un retraso de unos pocos milisegundos podría ser crítico, la capacidad de procesamiento local permite ajustes inmediatos, especialmente importante para aplicaciones remotas o de alto riesgo. Al reducir la latencia, las máquinas pueden autorregularse mejor, detener las operaciones si se produce una falla grave o transferir cargas de trabajo a otros sistemas en tiempo real.
La propiocepción y la robótica autoconsciente amplían estas capacidades al proporcionar a las máquinas una percepción similar a la biológica de la tensión muscular o la tensión articular. Los sensores integrados en los componentes mecánicos pueden percibir ligeras vibraciones, detectar pequeñas grietas y detectar el desgaste antes de que se agrave. La maquinaria responde de forma autónoma, aplicando menos fuerza, distribuyendo las cargas de forma más uniforme o indicando que una pieza necesita una pequeña revisión antes de que falle por completo. En entornos industriales de alto estrés, esta capacidad de percepción interna ahorra tiempo y dinero.
El Metaverso Industrial ofrece entornos digitales inmersivos. Al combinar datos en tiempo real, registros históricos y simulaciones basadas en IA, este ecosistema virtual permite que tanto máquinas como humanos practiquen la respuesta a diversos modos de fallo.
Las estrategias de mantenimiento pueden probarse y perfeccionarse en un entorno que refleja las operaciones reales sin riesgo de tiempo de inactividad ni daños. Este enfoque fomenta la experimentación y la rápida innovación en las prácticas de mantenimiento.
Otro avance es el mantenimiento orientado a la misión, donde los sistemas de IA deciden el mejor momento para las intervenciones según las prioridades operativas generales. Si una instalación funciona a plena capacidad, las tareas de mantenimiento no críticas pueden posponerse, mientras que los activos con mayor riesgo de fallos graves reciben atención inmediata. De este modo, se cumplen los objetivos esenciales de producción sin descuidar la seguridad ni el estado a largo plazo de los activos. Al integrar todos estos elementos tecnológicos en un marco unificado, las industrias pueden transformar el mantenimiento, de una tarea reactiva a una función activa y estratégica.
Aunque el mantenimiento cognitivo aumenta la autonomía de las máquinas, la experiencia humana es indispensable. Los sistemas de IA destacan en el reconocimiento de patrones a gran escala y el procesamiento de datos en tiempo real, pero los humanos poseen una conciencia contextual y un razonamiento estratégico que las máquinas no pueden replicar. El mantenimiento cognitivo busca complementar, no reemplazar, a los profesionales técnicos. La IA asiste analizando cantidades masivas de datos de sensores y proponiendo programas de reparación óptimos, mientras que los técnicos verifican estas recomendaciones y gestionan la resolución de problemas complejos.
Esta relación colaborativa se convierte en un ciclo de retroalimentación donde las acciones y decisiones humanas mejoran los modelos de IA con el tiempo. Cuando un técnico modifica una intervención recomendada o invalida una información generada por la IA, el sistema rastrea y aprende de ese evento. Gradualmente, los modelos predictivos se perfeccionan, reduciendo las falsas alarmas y fortaleciendo la confianza. El personal de mantenimiento comienza a centrarse en tareas de mayor nivel, como orquestar las interacciones de las máquinas, entrenar los sistemas de IA y garantizar que las sugerencias automatizadas no comprometan la seguridad ni las consideraciones éticas.
La intuición humana es especialmente valiosa para la evaluación de riesgos y la planificación a gran escala. Si bien las máquinas pueden analizar datos con rapidez y eficiencia, solo los operadores humanos pueden considerar matices como las regulaciones emergentes, el impacto ambiental y las estrategias organizacionales. En lugar de realizar innumerables comprobaciones repetitivas, los trabajadores se convierten en supervisores, estrategas y mentores de sistemas inteligentes. Juntas, la inteligencia humana y la inteligencia artificial forman un ecosistema de mantenimiento resiliente, capaz de responder a desafíos inesperados.
En el sector manufacturero, una planta automotriz aplicó modelos predictivos basados en IA a soldadores robóticos. Tradicionalmente, los robots seguían trabajando hasta el mantenimiento programado o hasta una avería. Gracias a un software de autoaprendizaje, las máquinas comenzaron a detectar desgaste, anomalías vibratorias y lecturas de sensores que indicaban fallos inminentes. El tiempo de inactividad de la producción se redujo considerablemente y los reemplazos de piezas se programaron con mayor precisión, lo que se tradujo en ahorros de costos, soldaduras de mayor calidad y menos retrabajos.
En el sector del transporte, un operador ferroviario europeo equipó su material rodante con sistemas de monitorización basados en IA. Los datos en tiempo real sobre las temperaturas de frenado, la tensión de los ejes y el estado de las ruedas permitieron integrar intervenciones proactivas en los programas operativos. Las tareas de mantenimiento que antes solo se realizaban durante las inspecciones periódicas ahora se activaban cuando los datos indicaban un riesgo elevado.
Casos Prácticos: Mantenimiento Cognitivo en Acción. En el sector manufacturero, una planta automotriz aplicó modelos predictivos basados en IA a soldadores robóticos. Tradicionalmente, los robots seguían trabajando hasta el mantenimiento programado o hasta una avería. Con software de autoaprendizaje, las máquinas comenzaron a detectar desgaste, anomalías vibratorias y lecturas de sensores que indicaban fallos inminentes. El tiempo de inactividad de la producción se redujo considerablemente y los reemplazos de piezas se programaron con mayor precisión, lo que generó ahorros de costos, soldaduras de mayor calidad y menos retrabajos. En el sector del transporte, un operador ferroviario europeo equipó su material rodante con sistemas de monitorización basados en IA. Los datos en tiempo real sobre temperaturas de frenado, tensión en los ejes y estado de las ruedas permitieron integrar intervenciones proactivas en los programas operativos.
Las tareas de mantenimiento que antes solo se realizaban durante las inspecciones periódicas ahora se activaban cuando los datos indicaban un riesgo elevado. La tasa de fallos en servicio se redujo significativamente, mejorando la fiabilidad y la seguridad de los pasajeros. El operador también observó una mayor eficiencia en la programación y un uso optimizado del material rodante. En el sector energético, los parques eólicos han adoptado el mantenimiento cognitivo mediante la monitorización de palas y turbinas mediante IA. En lugar de adherirse a intervalos de servicio fijos, las turbinas recopilan datos continuos sobre las condiciones del viento, los niveles de vibración y el rendimiento general. Posteriormente, ajustan automáticamente el paso de las palas o la velocidad de rotación para reducir la tensión durante condiciones climáticas turbulentas. Esto ayuda a prevenir fallos mecánicos catastróficos, aumenta la generación de energía y reduce los costes de mantenimiento.
Los operadores han reportado mejoras impresionantes en la producción anual de energía y la longevidad de los componentes. Estos ejemplos ilustran los beneficios tangibles de combinar análisis basados en IA, gemelos digitales cognitivos e intervenciones autónomas. En diversas aplicaciones, las industrias obtienen enfoques más seguros, eficientes y proactivos para el mantenimiento de sistemas complejos. Desafíos y el futuro del mantenimiento cognitivo.
A pesar de su potencial, el mantenimiento cognitivo se enfrenta a varias barreras. Un desafío reside en la explicabilidad de la IA. Muchos modelos de aprendizaje automático se comportan como “cajas negras”, generando recomendaciones sin justificaciones claras. Los profesionales del mantenimiento pueden ser reacios a confiar o actuar según las sugerencias de la IA que no comprenden del todo. Por lo tanto, desarrollar modelos interpretables e interfaces intuitivas es esencial para ampliar su adopción.
La ciberseguridad es otro problema urgente. A medida que las máquinas se vuelven más interconectadas y autónomas, aumenta el riesgo de ataques maliciosos. Proteger los datos confidenciales de los sensores, evitar el acceso no autorizado a los controles operativos y garantizar la integridad del sistema exigen medidas de ciberseguridad robustas y adaptables. Estrategias como la transmisión de datos cifrados y la detección de intrusiones basada en IA son útiles, pero este es un campo en constante evolución.
Los sistemas heredados también presentan dificultades. Muchas industrias dependen de infraestructuras antiguas con conectividad limitada o sensores obsoletos.
La transición al mantenimiento cognitivo implica inversiones significativas en actualizaciones de hardware, plataformas de software y capacitación del personal. La cultura laboral debe cambiar para adoptar la información basada en IA y nuevos procedimientos. Las empresas que se adapten a estos cambios se posicionarán para obtener mejoras significativas en su rendimiento, superando a aquellas que no se adapten.
De cara al futuro, los avances informáticos desempeñarán un papel fundamental. La computación de borde ya está mejorando la capacidad de respuesta de la inteligencia artificial, especialmente en entornos remotos. Tecnologías emergentes como la computación cuántica podrían acelerar enormemente el procesamiento de grandes conjuntos de datos, lo que permitiría el análisis predictivo casi instantáneo. A medida que estas innovaciones maduren, el mantenimiento cognitivo podría evolucionar desde su actual énfasis en la predicción de fallos hacia un ámbito de activos totalmente autoconservadores y autooptimizadores.
El mantenimiento cognitivo transforma la fiabilidad industrial al permitir que las máquinas anticipen, se adapten y prevengan sus propios fallos, lo que marca un cambio decisivo en las estrategias reactivas y dirigidas por humanos, hacia ecosistemas de sistemas autónomos e inteligentes capaces de autopreservarse. Sin embargo, la experiencia humana sigue siendo vital para supervisar estas operaciones. Los técnicos e ingenieros deben garantizar que los sistemas de IA se basen en realidades prácticas, estándares éticos y objetivos estratégicos. El resultado es una relación simbiótica donde las máquinas gestionan diagnósticos con gran cantidad de datos y ajustes rutinarios, mientras que las personas se centran en la resolución de problemas complejos y una coordinación más amplia.
A medida que la industria avanza hacia una mayor autonomía e inteligencia, el mantenimiento cognitivo desempeñará un papel decisivo en el futuro de la gestión de activos. Con el tiempo, las máquinas de autoaprendizaje, capaces de evolucionar continuamente, redefinirán los límites de lo que los sistemas industriales pueden lograr. El camino ha comenzado, y quienes adopten el mantenimiento cognitivo hoy podrán obtener una ventaja competitiva en resiliencia operativa, eficiencia y liderazgo tecnológico.
La IA se encuentra con la ingeniería :
una nueva era de mantenimiento La fusión de gemelos digitales cognitivos, IA y experiencia humana está transformando las industrias: las máquinas no solo informan los problemas, sino que los resuelven de forma autónoma.
Máquinas que piensan: El auge del mantenimiento cognitivo.
Desde la simple monitorización hasta la autoconservación, el mantenimiento cognitivo integra la concienciación y se adapta en tiempo real, garantizando que las máquinas no solo funcionen, sino que evolucionen.
De la avería a la brillantez.
Durante décadas, el mantenimiento significó reparar tras un fallo. Luego llegó la predicción. ¿Y ahora? Las máquinas piensan, deciden y se autooptimizan, redefiniendo para siempre la fiabilidad industrial.
La IA se une a la ingeniería: Una nueva era del mantenimiento.
La fusión de gemelos digitales cognitivos, IA y experiencia humana está transformando las industrias: las máquinas no solo informan de los problemas, sino que los resuelven de forma autónoma.
De Tron a la realidad: El auge de las máquinas autoconservadoras.
La frontera digital de Tron, que en su día fue una visión de ciencia ficción, es ahora una realidad industrial, donde las máquinas ya no esperan el fallo, sino que predicen, se adaptan y se autoprotegen. El mantenimiento cognitivo es el puente entre la inteligencia virtual y la autonomía real.
Robots con un sexto sentido.
Los organismos de control industrial ya están aquí. Robots de inspección con autoconciencia y controlados por IA escanean, predicen y actúan, manteniendo las industrias en funcionamiento sin intervención humana.
Del pensamiento a la acción: Los robots como la personificación de la inteligencia cognitiva.
Los activos ya no esperarán soluciones humanas. Los sistemas autónomos, impulsados por IA, supervisarán, repararán y optimizarán automáticamente antes de que surjan problemas.
Máquinas que se autoreparan.
Olvídese del tiempo de inactividad. Las máquinas autorreparables impulsadas por IA utilizan propiocepción e inteligencia adaptativa para detectar daños y repararse, incluso antes de que se produzcan fallos.
Texto: Prof. Diego Galar, Prof. Ramin Karim, Prof. Uday Kumar Fotos: Shutterstock y Sisteplant.
Fuente original: “Maintworld”
10 Competitive Technology Orbitals in a Cyber Factory
10 Competitive Technology Orbitals in a Cyber Factory
10 Competitive Technology Orbitals in a Cyber Factory
This website uses cookies so that we can provide you with the best user experience possible. Cookie information is stored in your browser and performs functions such as recognising you when you return to our website and helping our team to understand which sections of the website you find most interesting and useful.
Strictly Necessary Cookie should be enabled at all times so that we can save your preferences for cookie settings.
If you disable this cookie, we will not be able to save your preferences. This means that every time you visit this website you will need to enable or disable cookies again.
This website uses Google Analytics to collect anonymous information such as the number of visitors to the site, and the most popular pages.
Keeping this cookie enabled helps us to improve our website.
Please enable Strictly Necessary Cookies first so that we can save your preferences!
More information about our Cookie Policy