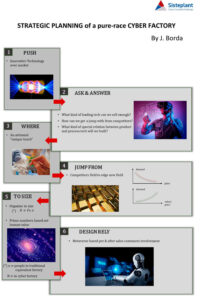
STRATEGIC PLANNING of a pure-race CYBER FACTORY
10 Competitive Technology Orbitals in a Cyber Factory
SHARE ON
Sisteplant nació en 1984 para ayudar al tejido industrial español a ser más competitivo. Crece a doble dígito y destina el 30% de su facturación a I+D+i, reinvirtiendo todo el beneficio en el negocio. Referente de la fábrica 4.0, es la autora de una herramienta de monitorización de las plantas que exporta a los cinco continentes. Ha desarrollado más de 4.000 proyectos de transformación, tiene 2.000 clientes y más de 300.000 usuarios. Hablamos con su CEO, Ana Santiago, de la necesidad de ir más allá. En esta entrevista reivindica que, para alcanzar resultados, además de las herramientas tecnológicas, “es necesario diseñar un plan de desarrollo humano con un enfoque holístico”.
P.-¿Cómo está contribuyendo Sisteplant a la digitalización de la industria española?
R.-Sisteplant lleva 40 contribuyendo a la mejora de la estrategia industrial española. Trabajamos en la digitalización de procesos productivos, así como la gestión de ciclo de vida de los activos. Replanteamos los medios de fabricación mediante la implantación de automatizaciones flexibles, redefinimos las estrategias productivas y rediseñamos organizaciones para lograr agilidad y rentabilidad en entornos de series cortas.
P.- ¿Cuáles son sus principales herramientas?
R.-Nuestra Suite Manufacturing Intelligence integra Prisma (GMAO), Captor (MES), Promind (Inteligencia artificial) e i-tracker (despliegue de objetivos y mejoras), una solución digital completa y avanzada. Más allá de la digitalización sin más, ponemos especial foco en el “para qué” y en el impacto sostenible en el negocio.
P.-¿Qué nota le pone a la industria española en cuanto a modernización?
R.-Si bien es cierto que se han dado pasos en los últimos años, hay mucho recorrido aún, especialmente en las Pymes. El principal reto es crear hojas de ruta consistentes que integren la incorporación de tecnología, digitalización, desarrollo del capital humano y sostenibilidad. Todo ello, con un objetivo claro: mejora de la competitividad, agilidad de procesos y capacidades de realizar personalización en masa.
P.-¿Cuáles son los retos más urgentes?
R.-Si hablamos de aspectos concretos, merece la pena mencionar la adaptación o flexibilización de procesos con tiempos de cambio muy reducidos, la incorporación de robótica colaborativa, células virtuales o el rediseño de los medios productivos para que los ‘layouts’ puedan ser reconfigurables.
P.-¿Y en lo estrictamente digital?
R.-Desde el punto de vista digital, es necesario mejorar la integración de las cadenas de suministro, mejorando la capacidad de reacción en tiempo real, sin olvidar poner foco en la ciberseguridad. Otro aspecto importante es desarrollar estrategias que contribuyan a un desarrollo sostenible: uso de energías verdes, mejorar la eficiencia de las instalaciones productivas… Nuestra industria tiene iniciativas en marcha, pero, por desgracia, muchas son forzadas, sin un claro convencimiento de la necesidad e impacto social y económico de éstas.
P.-¿Qué impacto está teniendo el reparto de los fondos Next Generation?
R.-Las diferentes iniciativas van avanzando a distinta velocidad sectorial, la burocracia es alta en unos casos, y en otros la falta de información sobre el acceso a los fondos dificulta el acceso a grandes empresas, pero sobre todo a Pymes. El impacto no es inmediato, aunque se materializará en la medida en que se consoliden los proyectos.
P.-¿Cómo se imagina la fábrica del futuro, de aquí a 20 años?
R.-Desde un punto de vista operativo extremadamente flexible y adaptable en tiempo récord. Digital desde su concepción, monitorizada en tiempo real, integrada aguas arriba y aguas abajo y con altas capacidades de predicción en todos los aspectos. Respetuosa con el medio ambiente en toda su cadena de valor, desde la concepción del producto hasta su desmantelamiento: descarbonizadas y eficientes, con un alto aprovechamiento de los recursos. Integrada por personas que potencian sus capacidades aprovechando exponencialmente la tecnología, personas que habitan en regiones con alta calidad de vida.
P.-¿En qué se fundamenta el modelo de organización y desarrollo de las personas en un entorno de manufactura avanzada? ¿Cuáles son las bases de vuestra metodología Human 4.0?
R.-Digitalizar y transformar nuestras fábricas no es suficiente para lograr el éxito, es necesario plantear un plan de desarrollo humano con un enfoque holístico, que contemple objetivos y metas tecnológicas, de negocio, y también aspectos relativos a la transformación del papel las personas: perfiles, competencias, funciones, áreas de conocimiento a desarrollar, organigrama, y modelo de relación con la empresa… para alcanzar el estadio Human 4.0.
P.-¿Cómo tiene que cambiar el organigrama de la empresa para asumir esa política?
Ese modelo alternativo de personas se apoya en organigramas planos, poco jerárquicos, y promueve el trabajo por proyectos para adaptarse a las demandas cambiantes del mercado. Personas motivadas desde el aporte de valor y la tecnología que configurarán equipos “aumentados” de alto rendimiento, con gran conocimiento de las claves del negocio gracias al soporte de la tecnología.
P.-¿A qué retos se enfrenta Sisteplant en este momento?
R.-Somos inconformistas con el statu quo por naturaleza. Actualmente, la evolución tecnológica avanza a velocidad de vértigo y, a pesar de que nuestra inversión en I+D+I es superior al 30% de nuestros ingresos, no siempre es suficiente para acometer todas las ideas innovadoras que queremos poner en marcha. Por ello, me atrevería a decir que ese es nuestro gran reto para garantizar nuestros planes de crecimiento de un 10-15% para los próximos años: mantener nuestra capacidad de innovación y su financiación en los horizontes temporales adecuados.
P.-¿Qué consejos daría a aquellas compañías que aún no cuenten con una estrategia de transformación digital?
R.-Los escenarios industriales futuros combinarán un incremento del peso tecnológico con un papel reforzado de las personas como alma del sistema. Los entornos TIC tradicionales no serán suficientes y requerirán un mayor desarrollo para convertirse en la inteligencia tecnológica de la planta, aportando conocimiento a todos los niveles. Dicho esto, es necesario apostar por soluciones escalables y dar pasos firmes y seguros.
P. ¿Cuál es la clave entonces?
R.-La estrategia digital bien estructurada es imprescindible, pero no podemos olvidar otros factores organizativos, humanos y medioambientales. La clave está en integrar todos ellos teniendo en cuenta que hay que ser realista y que la operativa en el corto plazo, debe financiar las actuaciones a medio y largo.
10 Competitive Technology Orbitals in a Cyber Factory
10 Competitive Technology Orbitals in a Cyber Factory
10 Competitive Technology Orbitals in a Cyber Factory
This website uses cookies so that we can provide you with the best user experience possible. Cookie information is stored in your browser and performs functions such as recognising you when you return to our website and helping our team to understand which sections of the website you find most interesting and useful.
Strictly Necessary Cookie should be enabled at all times so that we can save your preferences for cookie settings.
If you disable this cookie, we will not be able to save your preferences. This means that every time you visit this website you will need to enable or disable cookies again.
This website uses Google Analytics to collect anonymous information such as the number of visitors to the site, and the most popular pages.
Keeping this cookie enabled helps us to improve our website.
Please enable Strictly Necessary Cookies first so that we can save your preferences!
More information about our Cookie Policy